Micro Precision Injection Molding: Revolutionizing Manufacturing
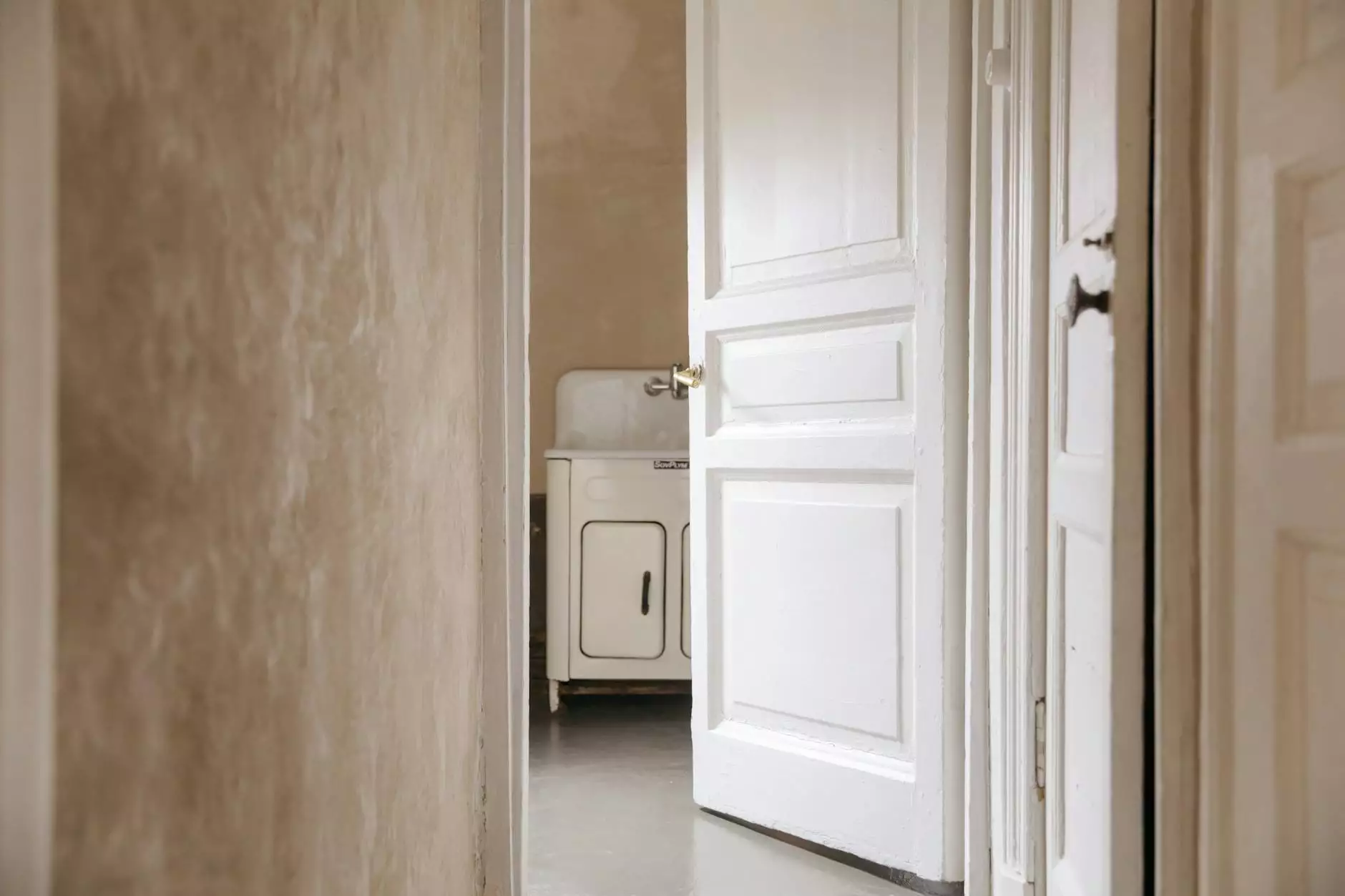
In the fast-paced world of manufacturing, micro precision injection molding has emerged as a game-changer, particularly for sectors requiring meticulous attention to detail and flawless component production. At DeepMould.net, we specialize in this cutting-edge technology, providing innovative solutions that meet the stringent demands of modern industry.
Understanding Micro Precision Injection Molding
Micro precision injection molding is a specialized process that allows for the production of intricate parts with micron-level accuracy. This technology is instrumental in sectors such as electronics, medical devices, automotive components, and aerospace, where precision is not just preferred but essential.
Unlike traditional injection molding, which focuses on larger parts and simpler designs, micro injection molding takes manufacturing to the next level by creating smaller, more complex geometries that deliver superior performance and functionality.
The Advantages of Micro Precision Injection Molding
- High Precision: The primary advantage of micro precision injection molding is its ability to produce parts with extremely tight tolerances. Components can be manufactured to dimensions in the micrometer range, ensuring they meet exact specifications.
- Reduced Material Waste: This process is highly efficient, utilizing less material than traditional methods, which is not only cost-effective but also environmentally friendly.
- Increased Production Speed: Micro injection molding allows for faster cycle times, meaning larger volumes of parts can be produced in a shorter timeframe, enhancing overall productivity.
- Complex Geometries: The technology facilitates the creation of complex shapes and designs that would be impossible to achieve using conventional methods.
- Enhanced Surface Finish: The parts produced have exceptional surface quality, reducing the need for additional finishing processes.
The Role of DeepMould.net in Metal Fabrication
As a leader in the field, DeepMould.net harnesses the power of micro precision injection molding to deliver superior metal fabricated components. Our commitment to quality and innovation sets us apart in the market.
Why Choose DeepMould.net for Your Micro Precision Injection Molding Needs?
Choosing the right partner for micro precision injection molding is critical to your manufacturing success. Here’s why DeepMould.net stands out:
- Advanced Technology: We invest in the latest equipment and technology to ensure that our injection molding processes are state-of-the-art.
- Expertise and Experience: Our team of skilled engineers and technicians brings years of experience to the table, ensuring that every project is executed flawlessly.
- Customization: We offer tailored solutions to meet the specific needs of our clients, whether they require small batches or mass production runs.
- Commitment to Quality: Quality assurance is integral to our process, and we implement rigorous testing protocols to ensure that every part we produce meets the highest standards.
- Competitive Pricing: With our efficient processes, we are able to offer competitive pricing without sacrificing quality.
The Process of Micro Precision Injection Molding
The process of micro precision injection molding consists of several key stages, each designed to contribute to the creation of high-quality components:
1. Material Selection
Choosing the right material is essential to achieving the desired properties in the final product. Common materials for micro precision injection molding include thermoplastics, which are known for their versatility and moldability.
2. Mold Design
Effective mold design is critical. Our team utilizes advanced software to create intricate mold designs that enable precise part shaping. The mold must be capable of handling high pressures and maintaining dimensional accuracy throughout the injection process.
3. Injection Process
During injection, the selected material is heated until it becomes molten and is then injected into the mold cavity under high pressure. This process allows the material to fill all corners and crevices of the mold, ensuring complete part formation.
4. Cooling and Solidification
After injection, the molten material cools and solidifies within the mold. This stage is crucial as it defines the final dimensions and surface finish of the part.
5. Demolding
Once the part has cooled sufficiently, it is removed from the mold. This process is monitored closely to prevent any damage to the part.
6. Quality Control
Finally, every manufactured part undergoes rigorous quality control testing, ensuring it meets all specifications before it's shipped to the client.
Applications of Micro Precision Injection Molding
The applications of micro precision injection molding are vast and varied, impacting numerous industries:
1. Electronics Industry
In the electronics sector, micro precision injection molding is used to create components such as connectors, housings, and insulators. These parts requirehigh levels of precision to ensure efficient performance and reliability in electronic devices.
2. Medical Devices
For the medical industry, micro precision molding plays a vital role in producing components for diagnostic devices, surgical instruments, and implants. The materials used in this sector are often biocompatible, and the precision of molding is critical for patient safety and device efficacy.
3. Automotive Components
In the automotive world, micro precision injection molding is essential for fabricating small yet critical components, such as sensors and connectors, that must endure harsh conditions while maintaining reliability.
4. Aerospace
Aerospace manufacturing relies heavily on precision. Parts created through micro precision injection molding are crucial for ensuring safety, performance, and compliance with stringent aviation regulations.
Sustainability in Micro Precision Injection Molding
At DeepMould.net, we understand the importance of sustainability in today’s manufacturing processes. Micro precision injection molding not only reduces waste but also allows for the use of recycled materials, contributing to a more sustainable manufacturing environment.
Innovations in Sustainability
- The use of biodegradable materials for certain applications.
- Energy-efficient processes that reduce the carbon footprint.
- Recycling initiatives that promote the use of reclaimed materials.
- Developing processes that minimize scrap and enhance reuse.
Conclusion: The Future of Micro Precision Injection Molding
The future of manufacturing is here, and it is precise. With advances in micro precision injection molding, companies like DeepMould.net are paving the way for the next generation of manufactured parts that meet the highest standards of quality and performance.
As industries continue to demand greater precision and efficiency, micro precision injection molding will play an increasingly important role. It not only meets the needs of today’s market but also addresses the sustainability challenges of tomorrow.
For manufacturers looking to stay competitive by embracing modern manufacturing techniques, partnering with experts in micro precision injection molding is essential. At DeepMould.net, we are committed to being at the forefront of this technology, ensuring that your business remains innovative and competitive.
Contact us today to learn more about how we can help you achieve your manufacturing goals through micro precision injection molding.