Plastic Mold Makers: Crafting Excellence in Manufacturing
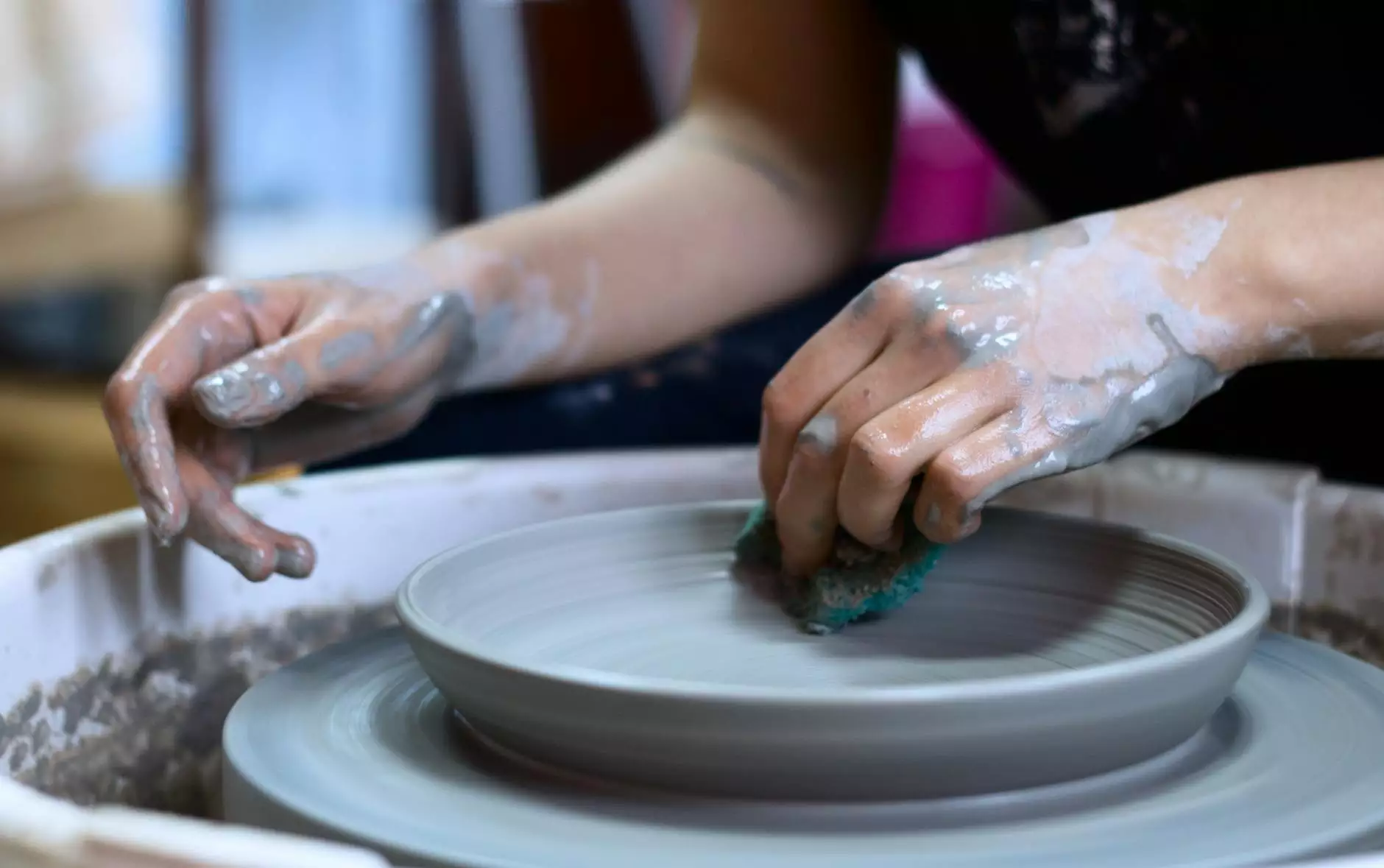
In the rapidly evolving world of manufacturing, the role of plastic mold makers cannot be overstated. These artisans and engineers are pivotal in transforming conceptual designs into tangible products. They utilize advanced technologies and traditional craftsmanship to create molds that ensure precision, durability, and efficiency in the production process. This article delves into the significance of plastic mold makers, the intricacies of the mold-making process, and how companies like Hanking Mould set benchmarks in the industry.
The Importance of Plastic Mold Makers
Every product that is molded from plastic starts its journey in the hands of highly skilled mold makers. The importance of plastic mold makers extends across various industries, including automotive, consumer goods, electronics, and medical devices. Here are some critical aspects pertaining to their significance:
- Precision Manufacturing: The complexity and precision required to create molds necessitate expert knowledge and skills.
- Cost Efficiency: High-quality molds reduce production time and waste, translating to lower costs.
- Innovation: Advances in mold-making technology have led to the development of unique and intricate designs, enhancing product functionality.
- Customization: Mold makers offer tailored solutions, adapting molds to meet specific client needs and product requirements.
The Mold-Making Process
The journey from an idea to a molded product involves several steps. Understanding this process can shed light on the expertise required from plastic mold makers.
1. Design and Analysis
The process begins with the design phase, where engineers collaborate with clients to understand their product needs. Tools like CAD (Computer-Aided Design) software allow for precise visualizations and simulations of the final product. At this stage, mold makers consider:
- The material to be used in the mold
- The complexity of the product design
- Production volume requirements
2. Material Selection
Choosing the right materials for mold construction is crucial. Common materials include:
- Steel: Preferred for high-volume production due to its durability and longevity.
- Aluminum: Cost-effective and suitable for lower production volumes.
- Specialty Alloys: Used for specific applications where heat resistance or other unique properties are required.
3. Machining and Fabrication
Once the design is finalized, the mold-making process shifts to machining. This step can involve:
- CNC (Computer Numerical Control) machining for precision cutting and shaping.
- EDM (Electrical Discharge Machining) for creating intricate details.
- Polishing to ensure a smooth finish, crucial for the quality of molded products.
4. Assembly
The assembled mold must be tested for quality and consistency. The attention to detail during this phase is what defines the expertise of plastic mold makers.
5. Quality Assurance
After assembly, several quality assurance tests are conducted, including:
- Dimensional verification to ensure specifications are met.
- Functional testing to ensure proper operation during production.
- Durability assessments to anticipate the performance of the mold over time.
Innovation in Plastic Mold Making
The landscape of manufacturing has changed dramatically with the advent of new technologies. Plastic mold makers are at the forefront, harnessing innovations that enhance efficiency and product quality.
1. 3D Printing
3D printing has revolutionized the initial stages of mold production. Rapid prototyping allows designers to create and test mold designs quickly. This reduces time and costs and allows for greater creativity in the mold design process.
2. Smart Manufacturing
Integrating IoT (Internet of Things) technology into machinery allows mold makers to monitor processes in real time, predict maintenance needs, and optimize production schedules. This leads to significant improvements in operational efficiency and product quality.
Challenges Faced by Plastic Mold Makers
While the profession is rewarding, plastic mold makers face unique challenges that require adaptability and innovation. Here are some common hurdles:
- Material Variability: Different materials behave differently under heat and pressure, necessitating ongoing education and experience.
- Cost Pressures: Budget constraints can limit the ability to invest in advanced technology, impacting quality and efficiency.
- Design Complexity: As product designs become more intricate, the demands on mold makers increase, requiring advanced skills and tools.
The Role of Hanking Mould in the Industry
Among the notable plastic mold makers, Hanking Mould stands out for its commitment to quality and innovation. With years of experience, they have established themselves as a leading plastic injection mould manufacturer. Their dedication to craftsmanship and customer satisfaction is illustrated in the following ways:
1. Expertise and Experience
The team at Hanking Mould comprises skilled professionals with extensive experience in mold design and manufacturing. Their expertise ensures that every product meets the highest standards of quality and performance.
2. Advanced Technology
Utilizing state-of-the-art machinery and software, Hanking Mould stays ahead of the curve. Their investment in technology translates into superior mold designs and faster turnaround times.
3. Custom Solutions
No two clients are the same, and Hanking Mould understands that. They offer personalized solutions tailored to the unique needs of each project, ensuring that every client receives a product that fits perfectly with their vision.
4. Commitment to Quality
Quality assurance is at the core of Hanking Mould's operations. Through rigorous testing and quality controls, they ensure that their molds are not only of high quality but also reliable in production.
Conclusion
In conclusion, the world of plastic mold makers is both complex and fascinating. These skilled professionals are essential to the manufacturing landscape, turning innovative designs into mass-produced products. Companies like Hanking Mould exemplify the high standards of quality, innovation, and customization that define success in the industry. As manufacturing continues to evolve, the expertise of plastic mold makers will undoubtedly remain a cornerstone of effective and efficient production.
Whether you are a business seeking to optimize your manufacturing processes or an individual curious about the intricacies of mold making, understanding the value of these craftsmen will enhance your appreciation for the art and science of manufacturing.